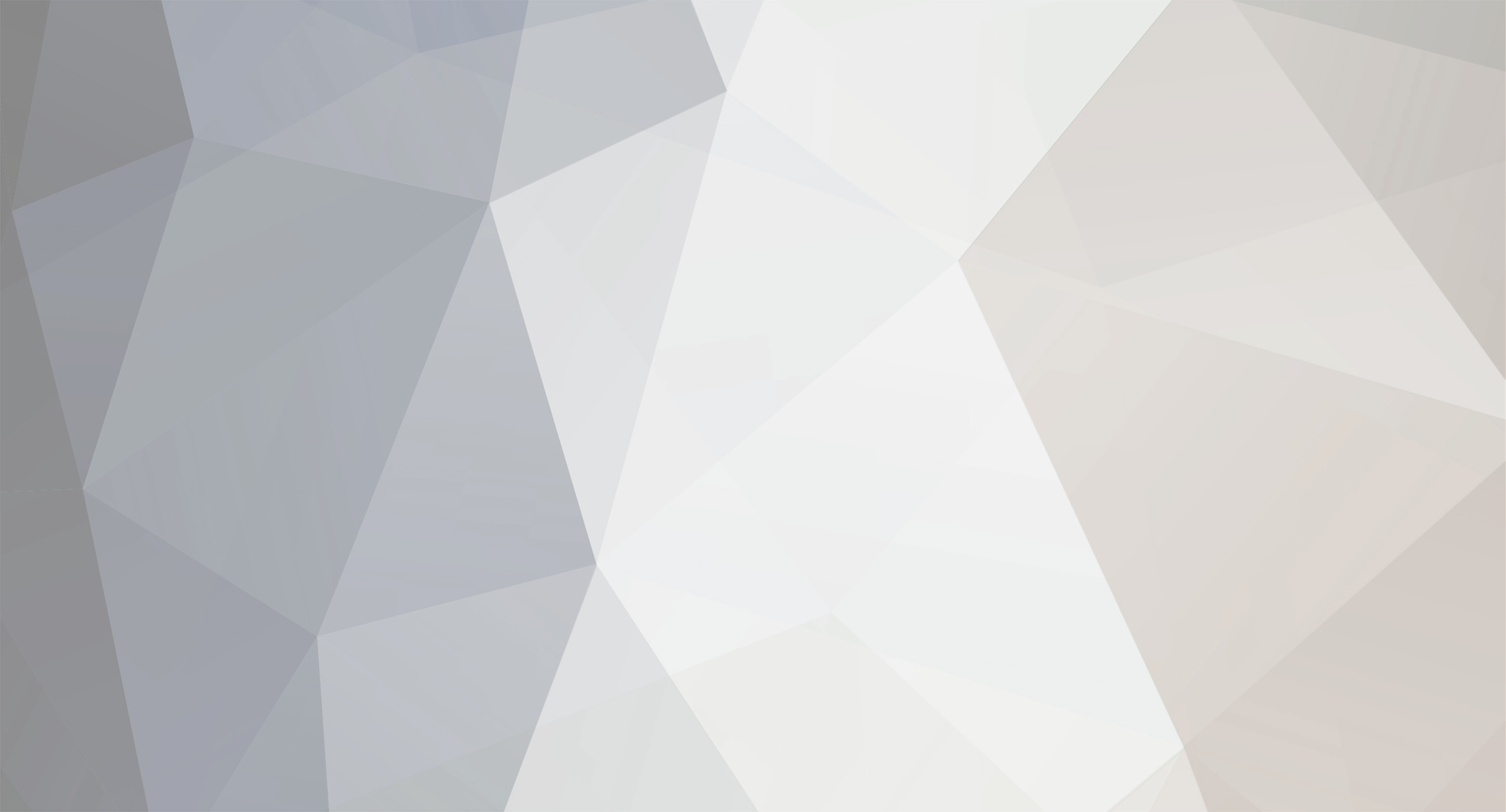
Wenig Bremse
Пользователи-
Постов
13 -
Зарегистрирован
-
Посещение
Весь контент Wenig Bremse
-
На какое-то время проект был задвинут из-за отсутствия свободного времени. Сейчас продолжил изготовление. P.S. Если эта тема все еще кому-то интересна дайте знать.
-
Вернулся из отпуска, в ближайште дни продолжу фотоотчет.
-
Есть еще один момент: для снятия размеров следующего слоя деталь нужно закрепить на месте, если начинать с дна, то проблем нет - положил четко напротив отмеченной линии и все, а вот если набирать горизонтальные слои, то тут надо сначала подумать как все это будет держаться. Не забывайте, что корпус не должен соприкасаться с кузовом, нужно оставить зазор в несколько мм, чтобы потом можно было нанести шумку. Еще раз повторюсь - для уменьшения количества слоев используйте более толстый материал, можно взять фанеру 18 или 22мм, толще не вижу смысла - тяжело обрабатывать и в конечном итоге будет много потерянного полезного объема.
-
От пола вверх. Я делал так: Сначала представил как должно выглядеть. Я для себя решил сделать лицевую сторону абсолютно плоской. Из картонки вырезал деталь, которая вставала на место лицевой плоскости (удалось ровно вырезать с 4го раза). Когда определился окончательно как будет стоять эта плоскость (немаловажно что в моем случае она перпендикулярна полу багажника - так проще делать слои). Затем малярным скотчем на багажнике отметил полоску по которой проходит лицевая плоскость, дальше сделал дно - это были самые сложнгые шаги, дальше все пошло проще. У меня очень мало свободного времени, поэтому последующие слои делал медленно, к тому же в гараже нет компа - приходилось ехать домой чтобы перенести на комп новый слой. В твоем случае проще - ты же ведь делаешь один единственный экземпляр - можешь по отмеренному трафарету резать фанерку и мерить следующий слой. Вобщем делай слои начиная от пола багажника, постепенно поднимаясь вверх.
-
Можно попробовать, на сколько я знаю ОСП гораздо прочнее ДСП и МДФ и не должен разваливаться при малой ширине стенки. К тому же у него толщина больше чем у фанеры (вроде бы 18мм, если не ошибаюсь) - будет проще изготовить весь корпус ввиду меньшего количества слоев. В любом случае я хочу попробовать все доступные материалы, но только после того как будет решен вопрос со снятием размеров, т.к. под каждую толщину материала нужно отрисовывать свою модель.
-
Я думаю от 1 до 3х слоев в середине для жесткости будет достаточно, но для начала надо определиться с месторасположением дина и уже отталкиваться от его размеров чтобы ребра были максимально широкими и эффективными. А три шестигранных "бошки" - это болты М6х30мм - применяются при склейке для центровки деталей, затем выкручиваются.
-
Если все же есть сомнения в качестве клеевого шва, то можно использовать клей ЭДП - эпоксидную смолу, шов на эпоксидке не будет вызывать никаких сомнений в своей прочности. И еще сразу хочу сказать про минусы данной технологии: 1. Плоские части из фанеры звенят (дно и лицевая панель). Чтобы с этим бороться нужно обязательно вводить в конструкцию ребра жесткости и испольковать виброизоляцию на основе каучуко-битумной смеси (обычный битум дубеет на морозе и не исполняет функцию виброгасителя). В идеале это 3-5мм на плоские детали - вибропласт и ему подобные материалы, и слой в 0,5 - 1мм на кривые поверхности - тут лучше всего подойдет каучуко-битумная мастика. 2. Фанера - это гигроскопичный материал - она впитывает воду, а в машине перепады влажности и особенно повышенная влажность достаточно частое явление. Вприципе битумная мастика защищает фанеру от этого, но всеже не лишним будет либо использование бакелитовой фанеры - шпон из которого она изготавливается полностью пропитан клеем, либо использовать различные пропитки типа пинотекса и пр., причем нормально такие вещи пропитать можно только под вакуумом и повышенной температурой - этот вопрос вполне решаемый в гаражных условиях. 3. Фанера по сравнению с ДСП, ОСП, МДФ - достаточно дорогой материал, кроме того расход материала достаточно большой, что неизменно скажется на стоимости готового изделия, хотя это всеже дешевле чем стеклоткань с эпоксидкой. Впринципе в данной конструкции не применяются саморезы и вполне возможно заменить фанеру на МДФ, но честно говоря незнаю каков будет результат - надо попробовать склеить несколько тонких деталей из МДФ и смотреть что из этого выйдет. Кроме этой технологии я рассматриваю еще как минимум 2 варианта изготовления, но для этого нужно сначала освоить фанерную технологию. Об этом расскажу как-нибудь позже.
-
Клеевого соединения более чем достаточно, более того оно получается прочнее, чем сама фанера - саморезы ненужны. Пока возможности нет. Но именно к этому я и стремлюсь. На сегодняшний день самая большая проблема - это снятие точных размеров и оцифровка модели, а уже отрисованный комплект всех деталей выразать можно за пару часов. Пока этот процесс делается вручную с трафаретами, лекалами и масштабно-координатной бумагой, из-за чего вобщем то за вечер получается замерить 1 слой (а больше свободного времени нет). Планирую в начале лета собрать устройство, позволяющее гораздо быстрее и более точно обмерять криволинейные плоскости. Как только вопрос снятия размеров будет решен и техпроцесс будет отлажен, тогда можно будет разговаривать о работах на заказ. А пока только могу понемногу постить фотки продвижения процесса.
-
еще фото: Извиняюсь за плохое качество - пришлось ужимать чтобы выложить на форуме. На корпусе видны следы клея - это всего лишь черновая сборка, поэтому на подтекший клей необращал внимания, да и потом это все скроется под слоем виброшумоизоляции.
-
Сегодня все таки пришлось идти в гараж и пользуясь случаем сделал несколько фоток того что склеино на сегодняшний день.
-
Объем заранее не просчитывал. Исходя из опыта других людей могу сказать что в моем случае объем должен получится в пределах 22-30 литров - такие объемы люди получая испольуя классическую технологию изготовления из стеклоткани и эпоксидки. Соответственно я рассчитываю уложиться в эти пределы. Когда модель будет полностью отрисована, то я смогу программно высчитать объем, а в реале лучше сначала покрыть стенки шумовиброизоляцией, а потом уже мерять объем водой. А после этого подбирать дин под такой или чуть меньший объем (уменьшить не проблема). Затем нужно покупать дин, мерять его реальные параметры, и если они будут отличаться (а они будут отличаться!!!) от параметров заявленных изготовителем, то необходимо корректировать объем корпуса, или брать другой дин . Как-то так. P.S. Параметры Тиля-Смола заявленные изготовителем как правило не всегда соответствуют (читай никогда не соответствуют) действительности, а немного отличаются от реальных. Это делается сознательно для того чтобы рядовой потенциальнгый покупатель вбил эти параметры в прогу и на выходе получил ауительно ровную АЧХ . К сожалению на сегодняшний день - это суровая действительность. Да, и еще пока фоток нет, и я думаю что сделаю тока после праздников, больше пока незнаю о чем еще рассказать. Если будут вопросы, то готов на них ответить.
-
Вот скрины 3D модели. Если кому то будет интересно, то после праздников выложу фото реального изделия ( на данный момент собрато 15 слоев)
-
Доброго времени суток. Меня заинтересовала эта тема и вобщем то решил пообщаться. В интернете полно статей как сделать "стелс" из стеклоткани/бумаги/прочего дерьма и эпоксидки или полиэфирки. Сам так делал - удовольствие весьма сомнительное, процесс геморный, длительный и совсем недешевый. В магазине смотрели как на ненормального когда я в 40й раз пришел покупать пару флаконов эпоксидки. чтобы сделать саб объемом около 25л с толщиной кривой стенки 10 мм у меня ушло чуть меньше 70 пузырей эпоксидки. Вобщем корпус получился далеко не самый дешевый. Сейчас занят изготовлением саба типа стеллс в крыло, но технология существенно отличается. Корпус представляет из себя около 50 слоев фанеры. Сразу оговорюсь - то что я делаю себе на данном этапе это всего лишь мастер-модель, которую я буду дорабатывать под коммерческое использование и мелкосерийное изготовление. Я постараюсь рассказать как сделать все это без применения заумных и дорогостоящих технологий. Итак для начала нам потребуется: 1. Картон пятитислойный (можно и тоньше, но главное чтобы был жесткий) 2. малярный скотч 3. карандаш 4. электролобзик 5. несколько листов фанеры ( я использую 9,5мм, но для ручного изготовления проще взять 16-18-22 мм) 6. клей для дерева 7. ножницы 8. 5-10 струбцин пока достаточно. Для начала нужно определиться с фронтальной стороной: если она будет гладкая, то ничего сложного нет, если будет иметь сложную 3D поверхность, то для начало надо "привязаться к гладкой плоскости, а потом выводить лицо. 1. Берем картон и вырезаем фигуру напоминающую форму дна нашего саба. постепенно подрезая лишние углы добиваемся того чтобы картонка улеглась наместо по возможности максимально повторяя все изгибы. Если отрезано слишком много то сверху это лепится малярным скотчем. Когда данный трафарет готов - кладем на фанерку, обводим, выпиливаем, меряем. Ели деталь вошла как надо то можно приступить к следующему слою. Достаточно на получившуюся деталь по краю доклеить малярный скотч в образовавшиеся пустоты - сдвиг будет как правило от 2х до 10мм. затем обводим это все на фанерке, затем от руки рисуем параллельную кривую, следя за тем чтобы толщина стенки получилась не менее 12-15 мм, лучше исходить из толщины 20-30мм. вырезаем получившуюся закорючку, обедетали кладем в багажник, снова скотч, обводка и т.д. 50 раз - при толщине фанеры 9,5 мм получите высоту 475мм. Вобщем это тоже гемор, но как мне кажется попроще возни с эпоксидкой, кроме того достаточно дешево. Почему не ДСП, МДФ и т.п. Потому что при такой маленькой толшине ДСП ломается, можно сделать только с толщиной стенки 30 и более мм, но потеряем в объеме. ДСП (лучше толстый - 45мм) нам понадобится в конце чтобы сделать лицевую часть. Я изготавливаю все это немного подругому, но суть таже, за исключением того что каждый слой хранится на компе и его можно отпечатать на плоттере и использовать в качестве трафарета. щас попробую сбросить несколько скринов отрисованной модели.